Transformer Reengineering Process Steps
Failure Analysis
Once the transformer is received at our factory, we start the failure analysis process with inspection of the tank and accessories as well as preliminary testing of the transformer. This is followed by removing the transformer lid and un-tanking the core and coil assembly. Throughout these steps we document the observations with photographs and copious notes.
At this point the more detailed forensic process begins with confirming the integrity of the core, lead structure and tap changer, if applicable. Then the preliminary electrical design effort begins to assist with developing the final inspection report based upon our discoveries. As part of inspection report, we will provide a quote, if needed, requesting a PO change order to address the additional repairs and any upgrade suggestions.
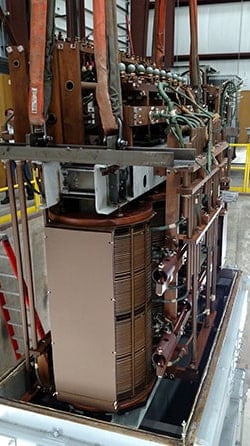
Engineering Redesign
Once the failure analysis process is completed and the final scope of work has been approved, we start the engineering redesign. The goal is to modernize the transformer components.
The redesign process incorporates an electrical short circuit analysis and improvements using the Andersen software program. We address any KVA increases and voltage changes being requested, including the opportunity to utilize NOMEX® insulation.
In parallel, any modifications or upgrades to the tank, which can include bushing locations or radiator replacements, are completed. Any modernization of monitoring gauges and controls is addressed.
We will also evaluate LTC repairs or retrofits, if necessary, into the complete redesign.
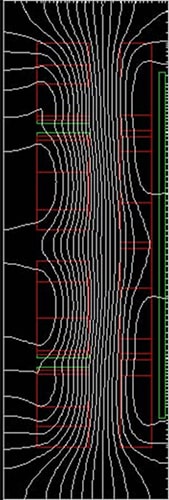
Winding New Coils
New coils are hand-wound in a temperature-controlled room by our team of experienced winders who have nearly a century of combined experience. We encourage you to visit our facility to see it for yourself.
Our hydraulic sizing presses allow us to precisely apply up to 200-tons of engineered pressure, to each coil, allowing us to obtain accurate overall completed electrical height and electrical center positioning to within ±0.125” (3mm) tolerances.
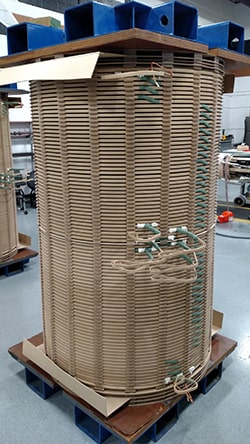
Assembly of Core and Coils
Most steel cores can be reused, saving you time and money. If it needs work, from minor repairs to a full redesign, we can do it.
Whether your core steel is reused, repaired, or replaced, every core is laid down, using our hydraulic core table to assure the safest and least harmful handling of your core steel. The frames and old core insulation are then removed, and a redesigned insulation package is installed in place of the old to assure the best possible core cooling and highest possible final core ground values.
Your new coils will be landed on the core in a temperature-controlled room. Once the core is assembled, the laborious process of installing the lead frame and attaching (crimping) the leads to the coils and LTC begins.
Once the process is completed, the assembly is wrapped to maintain cleanliness and dried in our specially-built oven before tanking.
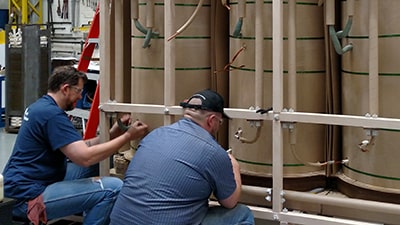
Remanufacturing LTC and DETC switches
Remanufacturing Load Tap Changers (LTC) and De-Energized Tap Changers (DETC) is a specialized process that involves restoring these devices to their original performance specifications. Companies like Quality Switch and Reinhausen have expertise in manufacturing high-quality switches and tap changers that are essential for controlling power in transformers. Quality Switch is known for its de-energized tap changers and electrical switches, while Reinhausen has been a pioneer in on-load tap-changer technology. Both companies contribute significantly to the reliability and efficiency of electrical power systems by providing components that ensure optimal voltage regulation and transformer performance.
-2.png?width=300&height=304&name=Untitled%20design%20(37)-2.png)
Controls
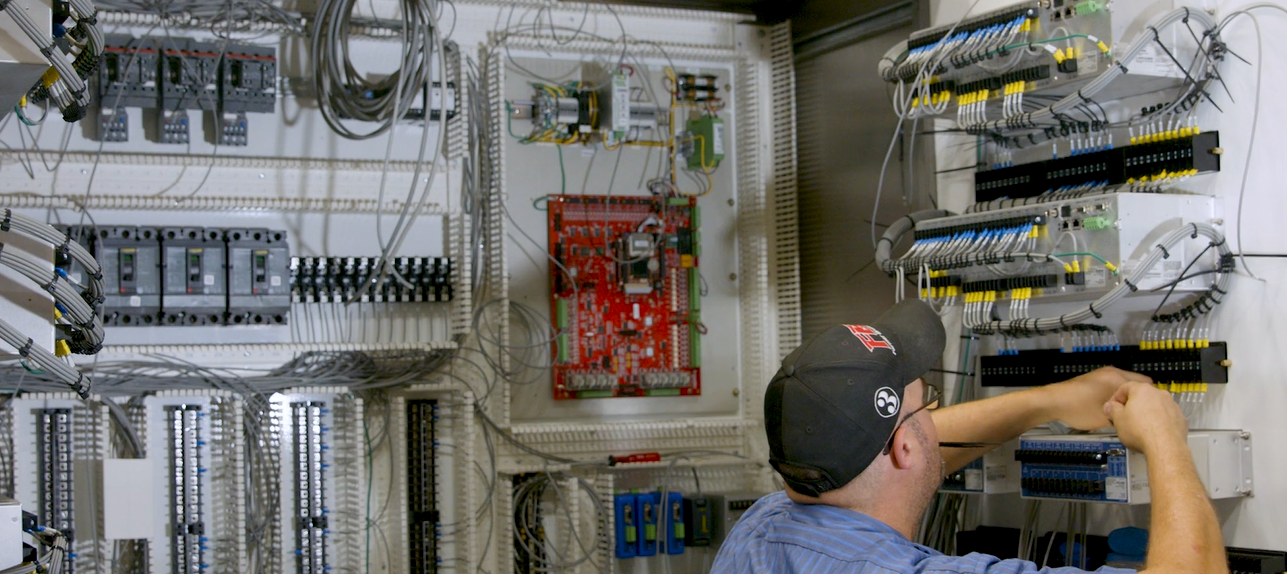
The control panel of a substation transformer is a critical component for monitoring and managing the transformer's operation. It typically includes SEL controllers, which are known for their reliability and advanced protection features. These controllers can be disc-based, providing robust control and monitoring capabilities. Additionally, the panel is equipped with Qualitrol gauges, which are essential for the continuous online monitoring of transformer health parameters, ensuring the transformer operates within safe limits and alerting to potential issues.
Tanking
Tanking a substation power transformer is “an accelerated” 1-day step in remanufacturing. We encourage customers to witness it during our pre-tanking process.
After drying “the core and coil assembly” the process of inserting the core and coil assembly “and connecting all of the leads” inside the tank begins immediately and is completed the same day.
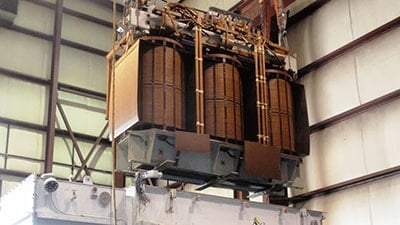
Oil Processing
Oil processing begins immediately after tanking is complete. The unit is placed under vacuum then filled with hot oil. The oil is then recirculated through the oil processor four times, filtering and heating it to ensure dehydration and degasification. Samples are taken and sent to an outside analysis lab, such as Weidmann, to confirm the oil meets ASTM & IEEE Standards and is safe and ready for testing.
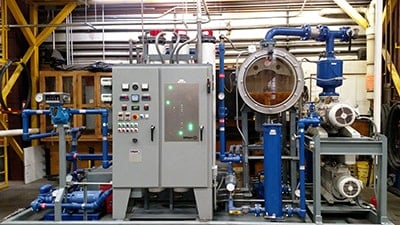