Reengineer Your
Power Transformer
Power Transformer
Why Remanufacturing Wins
Get your transformers in half the time OEMs can deliver
“They don’t make ‘em like they used to.” Your power transformer is valuable. Don’t throw that away: remanufacture, reuse, and save. In the 20th century, substation transformers were designed with reliability in mind—thick steel tanks, spacious tank interiors, and plenty of copper. This “greater design margin” approach kept power transformers running cooler, extending their life expectancy. Solid, older power transformers are the key to remanufacturing America’s power grid to be stronger than ever.
At Jordan Transformer, we specialize in rewinding and remanufacturing your power transformers with base ratings from 10MVA-80MVA and 69kV-230kV with complete Class II IEEE testing.
Value for You
Remanufacturing Power Transformer Process Flow
Freight
↓
Un-Tank
↓
Inspection
↓
FSOW Report
↓
Leads
↓
Controls
Rewind
↓
Core re-Build
↓
Radiators
↓
Assemble
↓
Tank*
Preliminary
↓
Full IEEE Testing*
* indicates typical customer witnessing opportunities during the process
Final Paint
↓
Freight
↓
Installation
Dedicated Remanufacturing Facility Capabilities
Rewinding means a custom rebuild for your unique transformer and substation requirements.
This effort requires and is performed in our dedicated 70,000 sq foot remanufacturing facility situated on 15 acres in Jordan, MN, which contains:
- Winding room environmentally controlled
- 9 specialized winding machines with an 80-ton and 200-ton coil sizing apparatus
- Core and coil assembly room temperature controlled
- Drying oven for completed coil assemblies
- Drying oven for completed core and coil assemblies
- Sandblasting booth, external dedicated building
- 8 separate oil tanks (total 40,000-gallon oil farm)
- 8 storage buildings for components in waiting
- 13 cranes and hoists
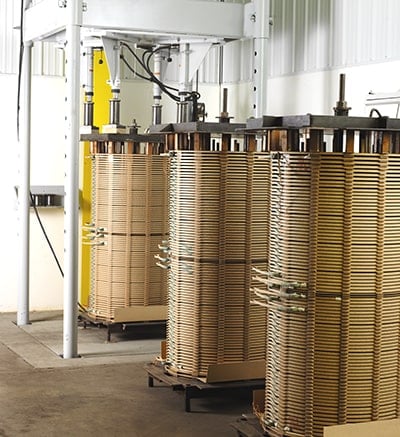
The dedicated high-bay has a 50-ft ceiling to accommodate medium to large power transformers. The bay includes:
- An 80-ton overhead crane
- A 50-ton overhead crane
- Two paint booths with high ceiling for transformers and components
- Hot oil processing system—customized for transformer application
- Welding cell 3,600 sq ft with 50-ft ceiling
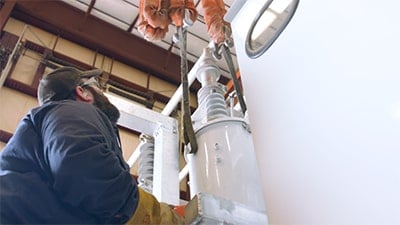
The dedicated test facility
- Impulse and partial discharge testing
- Impulse generator GTU 1000 kV - 50 kJ with SDA12-bit digital scope
- 300 kVA / 180 Hz generator with partial discharge monitoring
- 300 kV hi-pot transformer
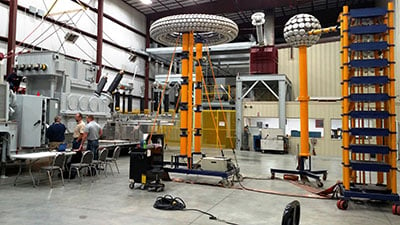
Experience Reengineering These OEM Transformers:
-
ABB
-
Allis-Chalmers
-
Brown-Boveri
-
Central
-
CG Power
-
CGE
-
Delta Star
-
Eastern
-
ELCO
-
Federal Pacific
-
Federal Pioneer
-
Ferranti-Packard
-
General Electric
-
Hevi-Duty
-
Howard
-
ITE
-
Delta Star
-
Kuhlman
-
MagneTek
-
McGraw-Edison
-
Moloney
-
Neeltran
-
Niagara
-
North American
-
Pacific Crest
-
Pauwels
-
Pennsylvania
-
Prolec
-
RTE/ASEA
-
Siemens
-
Sonmez
-
Standard
-
Tamini
-
Uptegraff
-
Virginia
-
Wagner
-
Waukesha
-
Westinghouse
Available Upgrade Options
Radiator replacements
Updated or new controls and wiring
75°C and 95°C insulation systems using Nomex® insulation
KVA potential increases
Voltage changes
Bushing relocations